How to Add a Prefabricated House Extension
At Cameron Construction, we’ve seen a growing interest in prefabricated house extensions. These innovative additions offer homeowners a quick and efficient way to expand their living space.
Prefab extensions combine the benefits of custom design with the convenience of off-site construction. In this post, we’ll guide you through the process of adding a prefabricated house extension, from planning to installation.
What Are Prefabricated House Extensions?
Types of Prefab Extensions
Prefabricated house extensions are pre-built structures manufactured off-site and transported to your property for quick installation. These extensions come in various forms, each with unique benefits:
- Modular Extensions: These complete room-sized units are built in a factory and delivered to your site. They offer the fastest installation time and minimal on-site disruption.
- Panelised Systems: These involve pre-made wall, floor, and roof sections assembled on-site. They provide more flexibility in design while still reducing construction time.
- Container Homes: Repurposed shipping containers offer a unique and eco-friendly option for those seeking a modern aesthetic. They’re particularly suitable for small extensions or standalone structures.
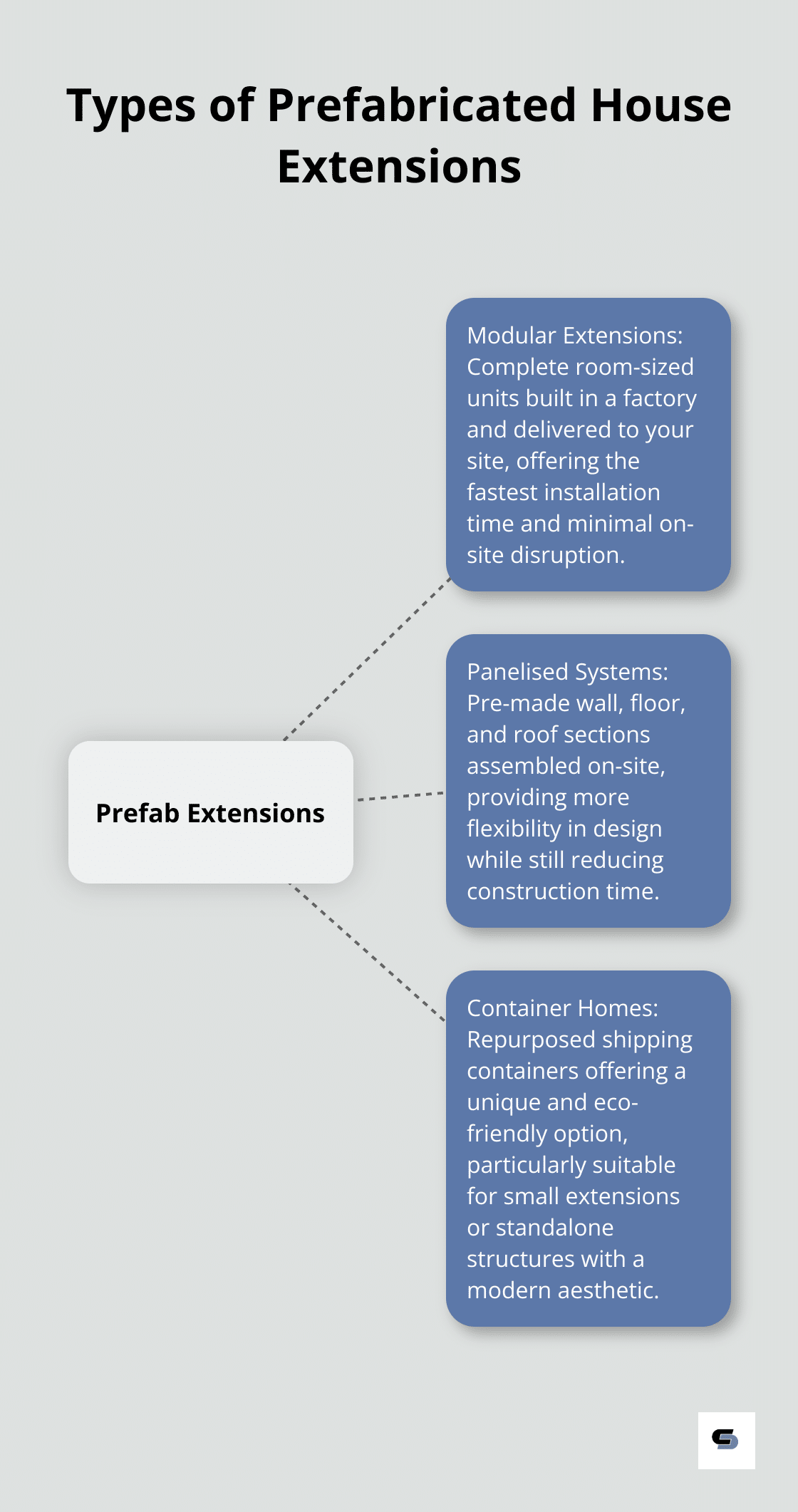
Advantages of Prefab Over Traditional Extensions
Prefab extensions offer significant advantages over traditional builds:
- Reduced Construction Time: What might take months with conventional methods can be completed in weeks with prefab. This means less disruption to your daily life and faster enjoyment of your new space.
- Superior Quality Control: Factory-controlled environments ensure consistent standards and minimise weather-related delays or damage. This controlled setting also reduces waste, making prefab extensions a more sustainable choice.
- Predictable Costs: The streamlined process of prefab construction helps avoid budget overruns.
Financial Considerations
While upfront costs for prefab extensions can be comparable to traditional builds, the real savings come from reduced labour costs and shorter construction timelines.
Energy Efficiency and Long-Term Savings
Prefab extensions often incorporate the latest in energy-efficient materials and design. This can lead to substantial long-term savings on utility bills.
Customisation Options
Despite being pre-built, prefab extensions offer a high degree of customisation. You can choose from a range of designs, materials, and finishes to match your existing home and personal style. Many manufacturers (including top choices like Cameron Construction) offer bespoke design services to ensure your extension meets your specific needs and aesthetic preferences.
As we move forward, it’s important to understand how to plan your prefab extension effectively. The next section will guide you through the essential steps of assessing your space, obtaining necessary permits, and choosing the right prefab manufacturer for your project.
Planning Your Prefab Extension Project
Assess Your Space and Needs
Start your prefab extension project by evaluating your current living space. Identify areas that need improvement and measure the available area for your extension. Consider factors like garden space, proximity to boundaries, and potential impact on neighbours. Determine how you want to use the new space – whether it’s for a home office, additional bedroom, or expanded living area. This assessment will help you choose the size and type of prefab extension that best suits your needs.
Navigate Permits and Approvals
Obtaining the necessary permits is a critical step in your prefab extension project. Local council requirements vary, so research your area’s specific regulations. Some prefab extensions may qualify for fast-track approvals, potentially saving you time and hassle.
In Melbourne, certain prefab structures under 10 square metres may not require a building permit. However, larger extensions typically need both planning and building permits. Consult with your local council or a professional builder (such as Cameron Construction) to navigate this process effectively.
Select the Right Prefab Manufacturer
Choose a reputable prefab manufacturer to ensure the success of your project. Look for companies with a proven track record in prefab construction and positive customer reviews. Ask for examples of their previous work and, if possible, visit completed projects to assess the quality firsthand.
When evaluating manufacturers, consider these factors:
- Customisation options
- Materials used and their quality
- Energy efficiency ratings
- Warranty and after-sales service
- Delivery and installation processes
Request detailed quotes from multiple manufacturers. This will help you compare costs and understand what’s included in each package. Some manufacturers might offer turnkey solutions, while others may require you to arrange additional services like site preparation or utility connections.
Plan Your Budget
Create a comprehensive budget for your prefab extension project. Include costs for:
- The prefab structure itself
- Site preparation (including any necessary excavation or foundation work)
- Delivery and installation
- Utility connections
- Interior finishes and fixtures
- Any additional landscaping or exterior work
Don’t forget to factor in a contingency fund (typically 10-15% of the total budget) for unexpected expenses.
Consider Timeline and Logistics
Plan the timeline for your prefab extension project. While prefab construction is generally faster than traditional building methods, you’ll still need to account for:
- Design and approval processes (which can take several weeks to months)
- Manufacturing time (usually 4-12 weeks, depending on the complexity of your design)
- Site preparation (1-2 weeks)
- Delivery and installation (often completed in just a few days)
- Final touches and inspections (1-2 weeks)
Coordinate with your chosen manufacturer and any additional contractors to create a realistic timeline for your project.
The next step in your prefab extension journey is the installation process. Let’s explore what you can expect when your new extension arrives on-site and how it will transform into a seamless part of your home.
How Does the Installation Process Work?
Site Preparation
The installation of a prefabricated house extension starts with thorough site preparation. This phase involves clearing the area of all unwanted vegetation, levelling the ground, and constructing a suitable foundation. During the process of grading, roots and other cellulosic materials should be removed from the building area. The foundation type depends on your specific extension and local soil conditions (options range from concrete slabs to raised foundations on piers).
For a typical 30 square metre extension, site preparation usually takes about a week. This includes any necessary excavation, pouring of concrete, and allowing it to cure. During this time, we also address any required drainage work to prevent future water issues.
Delivery and Placement
The arrival of your prefab extension marks an exciting milestone. Large trucks transport the prefabricated units to your property. Depending on the size of your extension, this could involve one large module or several smaller components.
A crane lifts each unit into place with precision. This process requires expertise and careful coordination between the installation team and the prefab manufacturer to ensure smooth delivery and placement.
The basic installation of a prefab extension often takes just one or two days. This speed offers a major advantage over traditional construction methods, which can disrupt your life for months.
Connecting Utilities
Once the prefab units are in place, the focus shifts to connecting your new space to your existing home. This involves linking up electrical systems, plumbing, and HVAC. The team also seals any gaps between the extension and your home to ensure proper insulation and weatherproofing.
Final Touches
The final stage involves adding finishing touches to perfect the space. This includes installing flooring, painting, and incorporating any custom features you’ve chosen. While much of the interior work is completed off-site, some on-site finishing is usually necessary.
The entire process, from site preparation to final touches, typically takes 2-4 weeks. This timeline is significantly faster than traditional extensions (which can take 3-6 months or more).
Communication Throughout Installation
Throughout the installation, the team maintains open communication with you. They provide regular updates and address any questions or concerns promptly. This approach ensures you’re always informed about the progress of your project.
While prefab extensions offer many advantages, working with an experienced company is essential. Their expertise ensures that your new space integrates seamlessly with your existing home, both structurally and aesthetically. If you’re considering a prefab extension, top choices like Cameron Construction can guide you through the entire process with their wealth of experience.
Final Thoughts
Prefabricated house extensions have transformed how homeowners expand their living spaces. These innovative solutions offer reduced construction time, superior quality control, and predictable costs compared to traditional methods. The energy efficiency and long-term savings potential of prefab extensions further enhance their appeal.
Careful planning ensures a successful prefab extension project. We recommend you assess your space, obtain necessary permits, and choose a reputable manufacturer with a proven track record. Create a comprehensive budget and consider the timeline carefully to ensure a smooth installation process.
At Cameron Construction, we have witnessed the growing popularity of prefabricated house extensions. Our team of experts can guide you through every step of the process, from initial design to final installation. A prefab extension offers a fast, efficient, and high-quality solution to your space needs.